Ethernet in Hazardous Locations
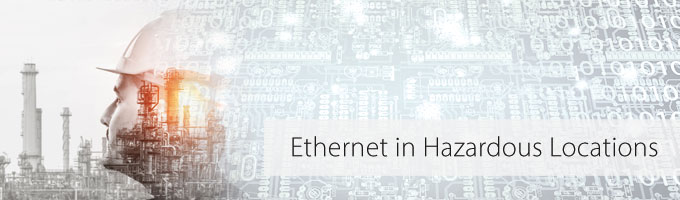
Ethernet in the Process Industry
Industrial Ethernet has been a vital networking and communication solution in factory automation for decades. Today, it is quite widespread. The process automation industry presents special challenges due to potentially explosive atmospheres, which have so far not allowed the use of Ethernet. These requirements include intrinsic safety, configuration in run, redundancies for maximum availability and a long cable length, which is limited to 100 meters for industrial Ethernet. When using Ethernet solutions in the process industry, it is important to distinguish applications where they will be used by their respective Zones.
Ethernet for Ex Zone 2
Turck offers its excom I/O system with Ethernet for installation in Zone 2. The system can pick up signals from Zone 1 or 0. To plug and unplug the Ethernet connectors at the gateway in run, users must ensure that the gateways are de-energized or work with a hot work permit. All other components such as power supply units, gateways or I/O modules can be exchanged during operation without a hot work permit
Ethernet for Zone 1
Using Ethernet in Ex Zone 1 is technically more difficult. With interlinked devices, it must be ensured that power levels do not add up. Today, a consortium of companies is working to overcome these hurdles and develop a standard for a two-wireIntrinsically Safe (IS) Ethernet. Communication and power supply take place over the same line. The future standard is usually referred to as Advanced Physical Layer (APL). However, these developments are not yet suitable for broad industrial use in Zone 1 (status 03/2020). One day, APL should enable Ethernet connections up to the field devices. However, classic 4 to 20 mA technology and I/O systems will continue to exist in parallel for cost reasons alone, even after APL has been established.
- Topics & Technologies
- Asset Monitoring Gateway with Cloud ID
- Asset Monitoring Gateway with SNAP ID
- Codesys
- Condition Monitoring
- Ethernet in Hazardous Locations
- Field Logic Controller
- Industrial Cloud
- Industry 4.0
- IO-Link
- Machine Safety
- Modular Machines
- Module Type Package
- Multiprotocol Ethernet
- Pick-to-Light
- Profinet
- RFID
- Safe work and Occupancy Monitoring
- Snap Signal
- Sustainability
- TAS – IIoT Service Platform
- The Visual Factory