Local News
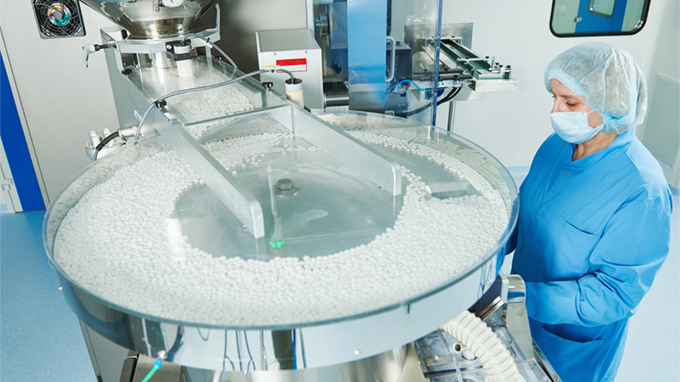
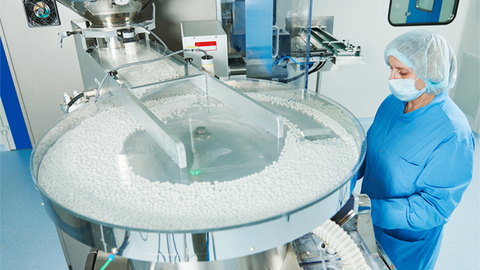
Access All Areas - Turck Banner’s Excom I/O System
The popularity of cooking programmes on television has encouraged millions of people to try out their culinary skills, particularly in baking and cake-making. However, failure to control certain parameters, such as time and temperature, can often result in a batch of dough or a cake mix being thrown away. Whilst these failures are annoying and frustrating, the financial impact is generally miniscule.
This same scenario of batch control failure, albeit magnified thousands of times over, can be seen in many industries today. Such failures and the resultant wastage often bring serious financial implications.
Industrial processes involve huge batches of ingredients that are often time and temperature sensitive. In the plastics industry, for example, a delay in the process prior to moulding can result in huge wastage costs.
Similarly, in the pharmaceutical industry the production of medicinal products requires the critical control of large batches of ingredients. With the value of a single batch often running into £millions, the control of all parameters throughout the process is vital.
High-speed, continuous throughput requires a process system that is not only fast and efficient but can also offer fail-safe, uninterrupted, operation.
To satisfy this demand, system builders and end customers in many industry sectors are benefiting from a universal I/O system that is highly regarded for Ex area protection but whose benefits extend to many non-ex applications.
Turck Banner’s Excom I/O family offers an I/O system with versions to satisfy all application ranges including –
- Non- ex
- Intrinsically safe circuits and installation in the non-ex area/zone 2
- Intrinsically safe circuits and installation in zone 1.
Customers benefit from component optimisation for particular zones and also from a standard configuration concept for periphery and field instrumentation. Common programming, regardless of application area, simplifies commissioning. Distinct terminal connection colours and clear labelling positively identify Ex and non-ex circuitry. Rationalisation across all zones brings cost saving through reduced inventory as well as an aesthetically pleasing uniform installation.
Module racks for 8, 12 and 24 modules afford high packing density and maximum flexibility, whatever the system requirements.
In terms of continuous operation, a key feature of the Excom system is the ability to hot swap power supplies and I/O modules. The unique power supply units were developed originally for use in hazardous areas as an alternative to the cumbersome EXD types. EXD power supplies cannot be disconnected during normal operation without obtaining a “Hot Work Permit” due to the risk of sparking when they are unplugged. The hot swap capability of Excom power supplies eliminates this problem.
Hot swapping is also a tremendous advantage in non-ex areas where continuous operation is required. The system can be serviced and changed at any time. The I/O modules, and the power supply modules, can be plugged and unplugged during ongoing operation, even in zone 1, without interrupting the field communication.
The Excom remote I/O system has been extensively tried and tested in the process industry and meets the high demands of equipment safety in that sector. The system allows a fully redundant set-up of the power supply, as well as communication interfacing. A choice of 24VDC or 230VAC is available and as a standard feature Excom also provides a system-redundancy solution for the bus structure. This allows the redundant Excom system to be connected via redundant busses to dual PROFIBUS masters.
As an additional service Turck Banner are able to supply fully pre-assembled Excom switch cabinets, either with standard variants or with additional fitted components to customer specifications, this offers two distinct advantages. Firstly, the customer receives system approval for the entire cabinet and secondly, proof of intrinsic safety for the complete system.
Modern industrial processes demand continuous operation, high throughput and, consistent quality. The many features of the Excom system, coupled with its suitability for operation in all areas is meeting this demand across a wide range of industry sectors including, food, pharmaceutical, packaging and plastics.